What We Do
-
MIM
-
GSG
-
TRANSMISSION
-
THERMAL

Metal Injection Molding
Solution Provider
With decades of technical experience, we have developed more than 2000 customized MIM products for different markets and applications.
Learn More
Gian Soft Goods
We are an innovative manufacturing solutions platform. GSG business unit mainly focus on soft material Design & Manufacturing, we can provide the ODM and OEM solutions and manufacturing facility with better cost optimization and achievements. Main Applications: Smart phone, speaker, smart watch and related 3C products .
Learn More
Precision Transmission
System Solution Provider
Precision Transmission System Design & Manufacturing; ODM、OEM Lean Production & Cost Optimization; Main Applications: Smart phone, Smart Wearable, Smart Home & Appliances, Automotive Electronics.
Learn More
Thermal
Solution Provider
With decades of thermal technical experience. we can provide customers with cost optimization solutions for parts. We can provide solutions for Consumer electronics, 5G Communication Base Station, Server, Projector, AR / VR, Customized parts and molds.
Learn More
- MIM
- GSG
- TRANSMISSION
- THERMAL
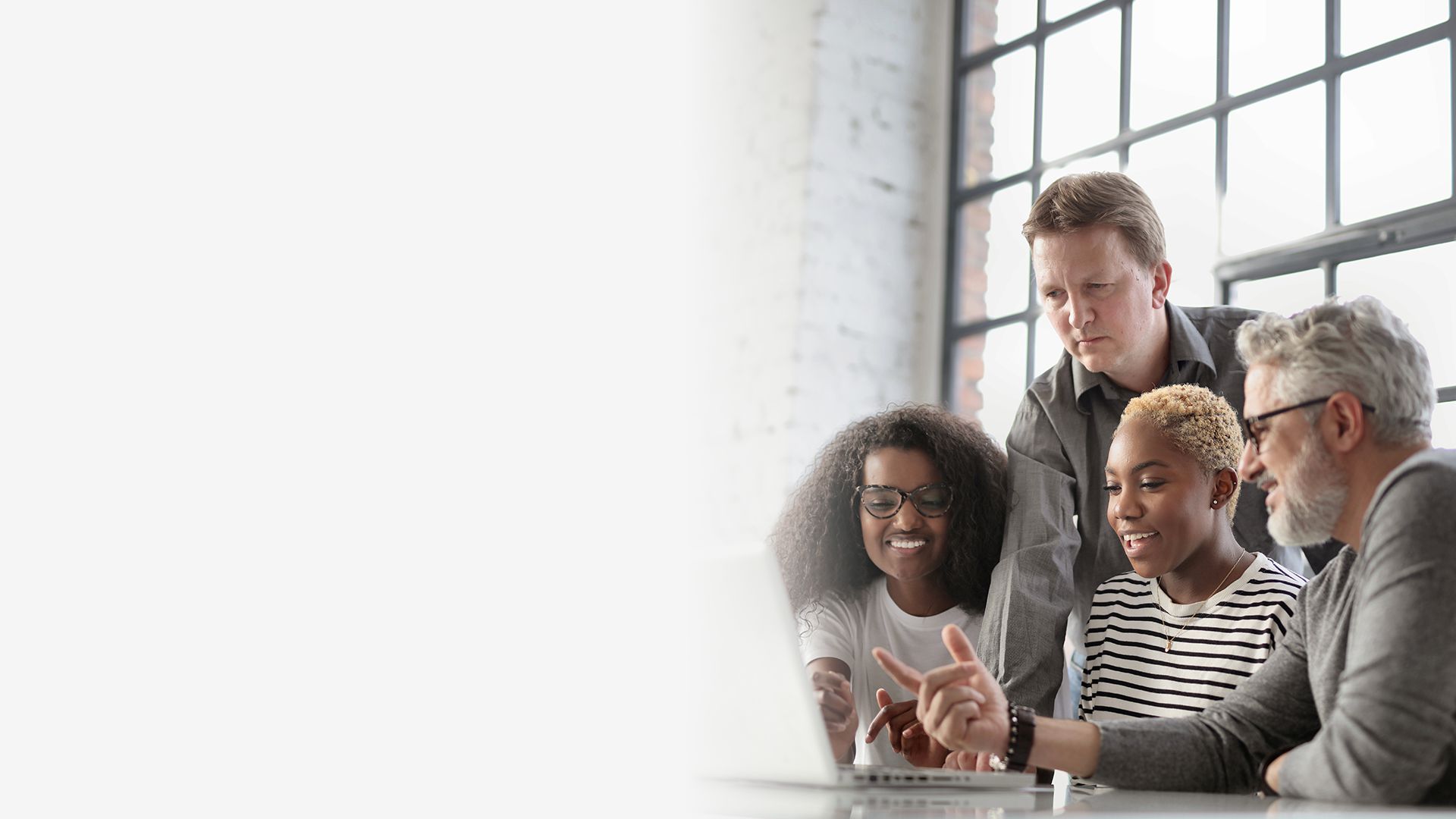
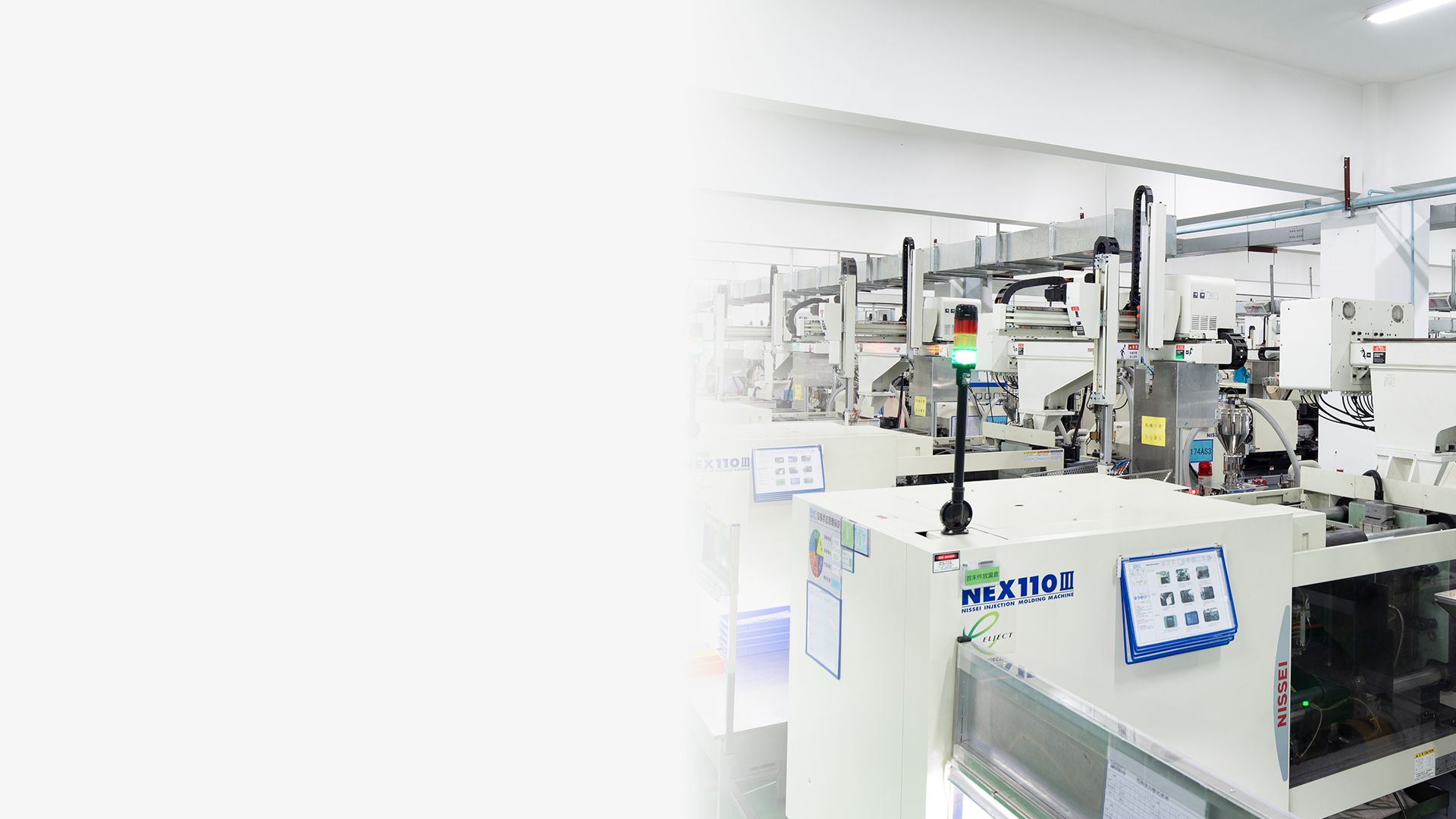
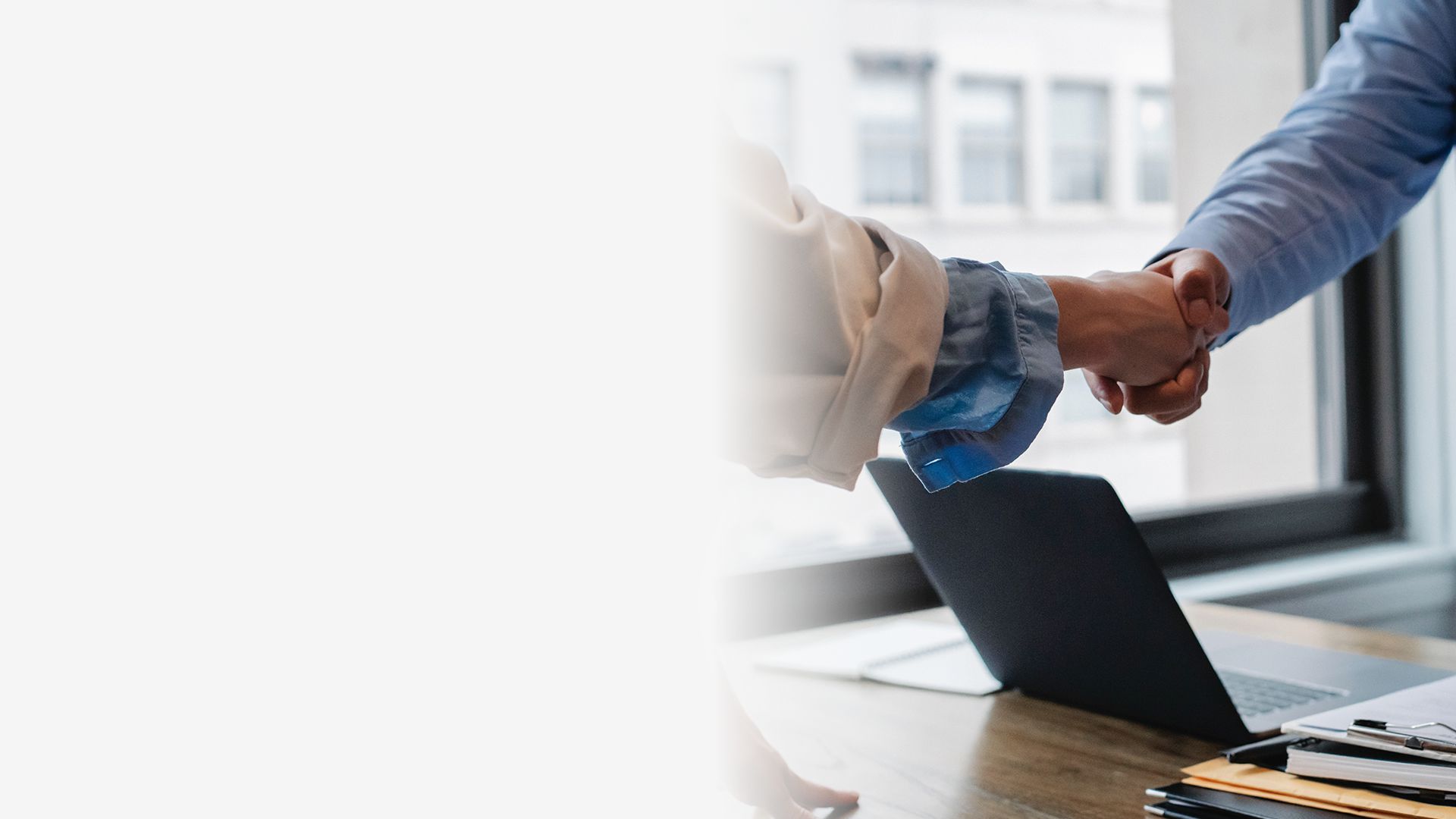
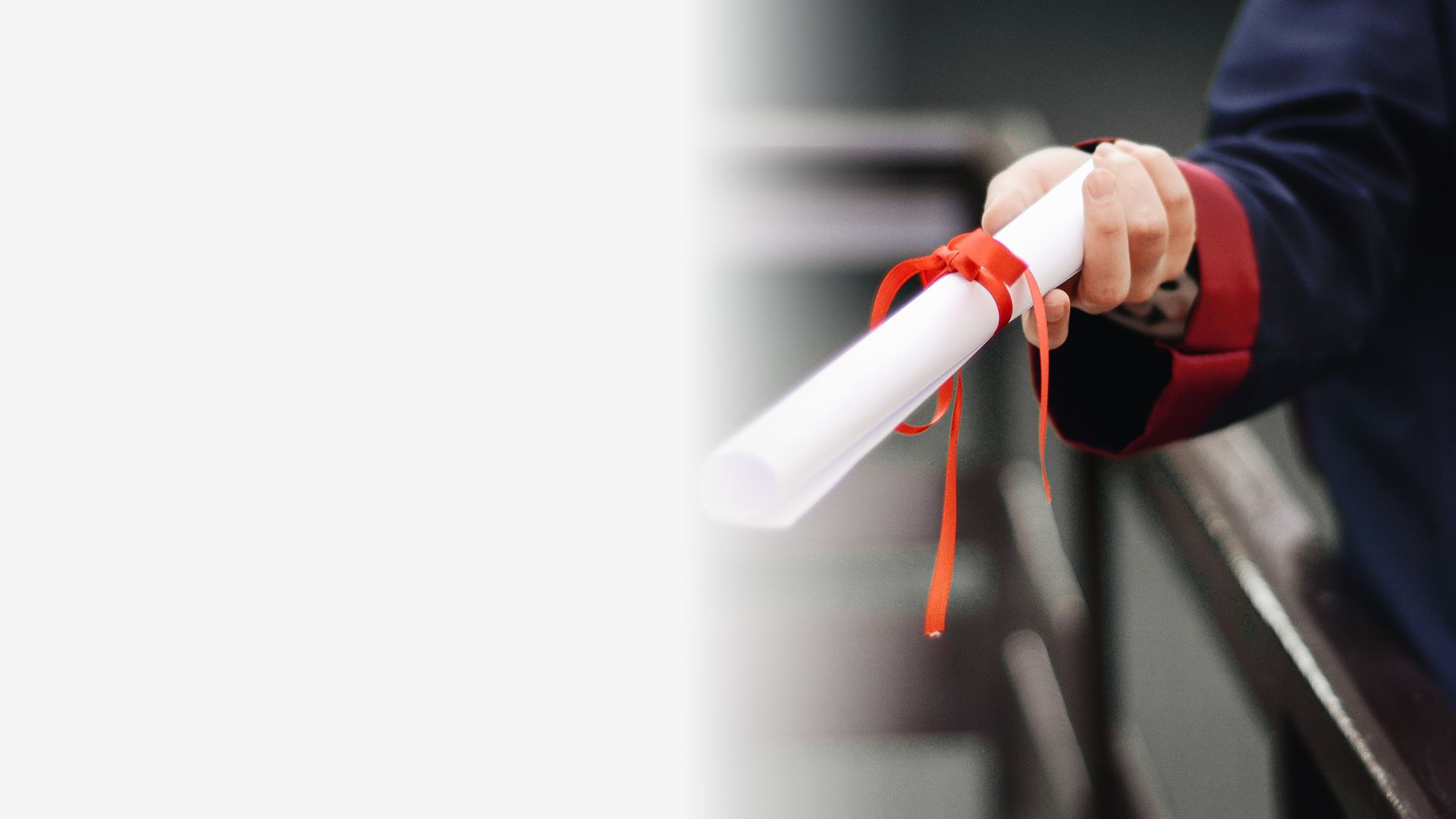
Social Responsibility
News
Why Choose Us
Gian provides a large quantity of metal materials structure, function and appearance in high precision, complex shapes and high performance. Besides, Gian is capable to develop ceramic and titanium alloy, to satisfy different customers' demand. Gian made heavy investment in furnaces, now Gian has both Japanese Shimazu vacuum.